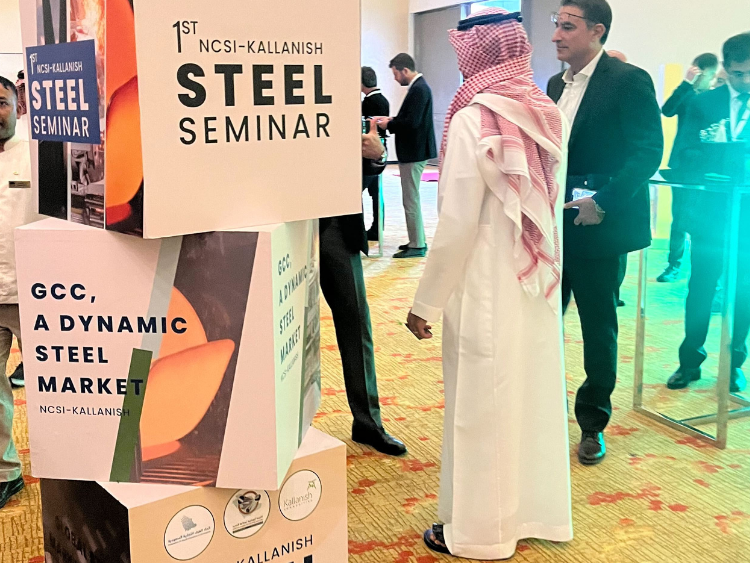
Saudi Arabia must upgrade IF steelmaking sector: NIDC
Saudi Arabia must reform its induction furnace steelmaking sector to boost the quality and economic efficiency of its steel industry, Khaled Al-Hajiri, vice president of building materials at the National Industrial Development Centre (NIDC), said at the 1st NCSI-Kallanish Steel Seminar in Riyadh on 16 September.
Scale, capacity utilisation, and lack of secondary steelmaking are the key issues for the sector. Al-Hajiri recommends a stricter regulatory framework, and avoidance of any new IF-based commodity rebar projects.
Stringent measures for quality control and safety, including radiation gates, are also needed. “We are not talking about stopping plants that are running,” he explained, “but about how to regulate and ensure they meet industry standards.”
When delegates asked whether induction furnace steelmakers had the financial capability to invest in upgrading their plants, Mohammed Al Jabr, steel expert and independent consultant, noted that “as long as it is agreed that there is a business case … the funds can be available.” He added that, in addition to private capital, there was support from government funds to upgrade industrial capacity.
Saudi induction furnace capacity has quadrupled to 4 million tonnes/year, and the number of furnaces has tripled over two decades. However, effective capacity is only 2.8m t/y because of inefficiencies. Another 30% increase in IF capacity is expected based on current projects. There are 26 IF producers feeding rebar and light sections mills, Al-Hajiri notes. IFs now account for some 30% of total Saudi steelmaking capacity.
However, because they have no refining technology, the quality of IF steel depends entirely on the quality of scrap. This means they are often unable to meet standard certifications for the region, and are not suitable for the mega projects that are now driving steel demand growth in Saudi Arabia.
There are also licencing and regulatory issues, as plants have been built with higher capacities than the licences they received, or have completed brownfield expansions without the correct permissions.
IFs are also a drag on energy efficiency, with the average Saudi IF consuming around 650 kWh/tonne of steel, compared to around 400 kWh/t for an EAF using 90% scrap. An NIDC study also found some plants that were extremely inefficient, consuming 725 kWh/t.
Globally, Al-Hajiri noted that China eliminated commercial induction furnace capacity in 2017; India, however remains the largest user of the technology with 35.2mt of crude steel production from IFs in 2022, or around 30% of total output.
Truly global, user-friendly coverage of the steel and related markets and industry that delivers the essential information quickly while delivering on most occasions just the right amount of between-the-lines comment and interpretation for a near real time news service of this kind.
Anonymous
Very good overview of the weekly steel market.
Anonymous