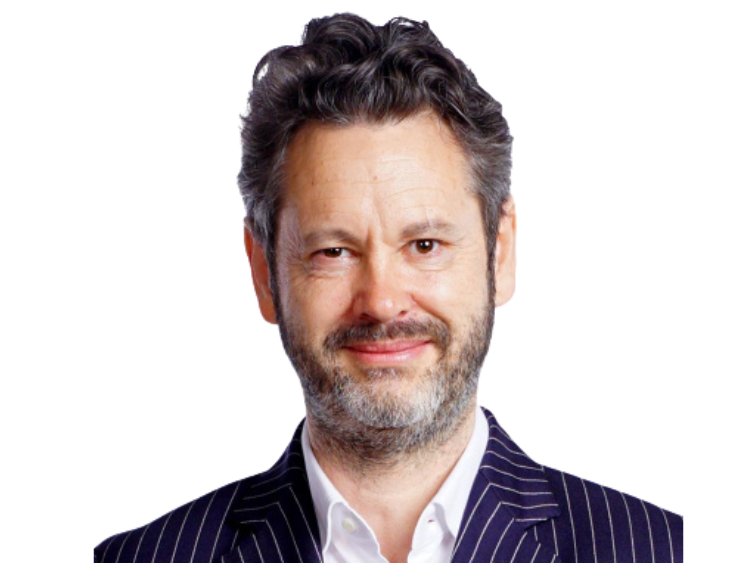
Q&A with Altilium’s COO and co-founder: Christian Marston
As Mario Draghi suggests Europe should create a single market for waste and recycling, to improve its circular economy, Altilium Clean Technology seeks to be the first to market and largest player in the UK’s battery recycling industry.
The UK-based firm, which has just celebrated four years, is preparing a Series B fundraise to speed and scale up. By recycling critical minerals from existing waste streams, Altilium is minimising the need for primary mining. Yet, its proposed business model goes beyond recycling.
It intends to produce cathode active material (CAM) and precursor CAM (pCAM) in the northeast of England, offering a closed-loop solution to the EV battery value chain.
Kallanish spoke with Altilium’s co-founder and chief operating officer, Christian Marston, to catch up on the company’s latest breakthroughs, ongoing developments and future plans.
➡️ What is Altilium’s mission in the battery recycling industry? As a co-founder, I’m interested in using material science to help solve the challenge of getting to net zero. Batteries are a unique proposition because you can recycle them with very high efficiencies. Our process can recover over 95% of the lithium, nickel, cobalt and manganese, and 99% of the graphite, and we can do that indefinitely. What we’re trying to do at Altilium is give the UK a domestic, non-Chinese, sustainable, low carbon source of critical materials. There’s a lot of geopolitics around critical materials but also this is about decarbonisation. We’ve done an LCA [life cycle assessment] and for CAM produced from recycling in the UK at our planned plant in Teesside, the carbon will be over 60% lower than CAM coming from China. That low carbon piece is very important for automotive OEMs, who have targets for stripping out carbon in their supply chain. Ultimately, the battery is a big contributor to the carbon in an EV. If 50% of the carbon in an EV battery is coming from the CAM, a newly produced EV could have 20% lower carbon if you use recycled material in that battery. What we’re focused on is being first to market in the UK and doing it at scale. Our aim is to be the largest player in the UK’s battery recycling industry and our focus is on full battery circularity – from end-of-life battery collection and production of black mass through to chemical refining to battery-ready p-CAM and CAM. |
➡️ Tell me about the company’s latest achievements. What are you working to accomplish this year? In terms of the technology, we’ve achieved a number of breakthroughs this year and we’ve filed a number of patents in the UK. One recent success is we’ve recovered over 97% of the lithium from LFP [lithium iron phosphate] batteries at our pilot line in Devon. We’re always looking at how we make battery recycling more economical. This is particularly important for LFP, because there’s more LFP coming but these batteries don’t have nickel and cobalt. We also look at how can we get a payable on the graphite, to improve the economics. Now we’re starting to qualify our materials in cells with various partners. We have a programme with Nissan, for example, which is backed by the APC [Advanced Propulsion Centre]. We’re producing CAM from recycled batteries and production scrap, then producing coin and pouch cells to compare the performance of recycled material with virgin material. We have another project to produce cells with UKBIC, which is supported by the Faraday Battery Challenge. We will supply high volumes of CAM for an NMC 811, a very high nickel battery chemistry. UKBIC will produce cells for qualification against their standard cells. This is the first time we will see how our material behaves in a gigafactory; and what it looks like when we coat it on an aluminium foil. We’re just preparing our first batch of CAM to be sent to UKBIC and they will produce the cells in Q1 of next year. We also completed a Series A raise earlier this year raising $12m from SQM, one of the largest lithium groups in the world. They’re supporting us in a lot of ways, including engineering support, and how we scale up. We’ve started a Series B as well. In the near future, we will have some other strong multinational strategic partners to help us speed up and scale up. |
➡️ What technology is Altilium adopting to recycle batteries and produce CAM? How does it differ from existing technologies? We’re innovating and developing IP at each part of the battery supply chain but our core competence is around the hydrometallurgical processing, from black mass to a battery-ready CAM. Unlike existing pyrometallurgical recycling processes, which are inefficient and cannot capture the whole value of the battery, our EcoCathode™ process allows us to recover over 95% of the lithium, nickel, cobalt and manganese, almost indefinitely, in a format that can be directly reused in battery manufacturing. There are several uniquenesses to our process and we filed our first patent in the UK earlier this year. The process is tailored to accommodate every battery chemistry, as well as gigafactory scrap and even primary nickel. We also have a low sodium flow sheet. We’re also upcycling. For example, we’re taking old Nissan Leaf batteries, which is an NMC111 chemistry, and we’re taking some production scrap. Then we recover the critical minerals but we also re-engineer and create a very modern chemistry, like NMC811, which a customer can use to build a new battery. By recycling to CAM, we capture more value of the critical materials, as CAM is the most expensive component in EV batteries. It also allows us to offer customers full battery circularity, where we collect the end-of-life battery and return the CAM to build a new battery. But CAM is a very specialised chemical product which needs qualification. That’s the reason we’re doing the work we’re doing with cells. |
➡️ Where are you developing and piloting the technology? When do you expect to be able to scale up and produce the first CAM samples? In Devon, we have our pilot line, Act 1, where we’re developing our green processing technologies. The work we’re doing there is around the flow sheet development. We’re already producing CAM samples for qualification and commercial engagement with various stakeholders. Our mini-commercial facility (Act 2) is being built in Plymouth and will finish later this year. This will process one EV battery per day and produce larger volumes of CAM, pCAM and battery salts for qualification with OEMs. We also have an existing hydromet plant in Bulgaria (Act 3). We will retrofit that to produce a battery intermediate product. This will process 8,000 t/y of black mass and produce a nickel MHP [mixed hydroxide precipitate] and lithium sulphate. Act 1, 2 and 3 are all part of the scale-up to mega-scale battery recycling at Act 4, our planned Teesside plant. |
➡️ How’s the Teesside project moving? When can we expect an FID and first production? The plan for our Teesside plant (Act4) is for it to begin production in 2027. We completed a feasibility study with Hatch last year and our Series B fundraise will support this next stage of our scale-up, which will be one of the largest green infrastructure projects in the UK and Europe. The next steps for us will be finalising the land, then planning and permitting, and building the team, we’re identified the ceo of that project. Then, we have further engineering studies to do and we’re engaging with the engineering consultants on that. The plant will have capacity to process battery waste from 150,000 EVs and this will produce 30,000 t/y of a battery-ready CAM. The plan is for this to probably be built in a modular way, so essentially the refinery will be two plants. The first will produce the battery metal salts and the second plant will produce the pCam and CAM. |
➡️ What are your plans to secure feedstock now and in the future? Will the refinery prioritise certain batteries and/or sourcing regions? We recently completed an engineering study with Hatch for our first commercial-scale battery recycling plant, which will also be located in Teesside. This will have capacity to process a mixed feedstock including LCO [lithium cobalt oxide battery] consumer scrap, LFP and NMC batteries and production scrap, for an output of 40,000 t/y of black mass. We started with the hydromet piece but we’re going to have to produce black mass as well. This will ensure we have a high-quality feed for our refining facilities. We see that in the future, black mass won’t be exported from the UK. It’s almost a strategic asset of the UK. Our feedstock is coming from various sources in the UK and even from Europe. The feedstock for the work we’re doing with UKBIC is coming from an automotive OEM. We have NMC batteries, old and newer chemistries, and we have some production scrap, because we want the nickel from the more modern chemistries. We’re also taking batteries from partners such as Synetiq and we’re even getting them from second life BESS [battery energy storage system] through our partnership with Connected Energy. The ecosystem of battery recycling is extending, now we’re talking to insurance companies. They want to make sure there’s a sustainable solution if a battery comes to a premature end-of-life due to a car accident. We can process it and put the materials back into a UK supply chain. |
➡️ How will OEMs cope with upcoming EU regulations on recycled content requirements? Do you believe there will be enough recycling capacity in the region to meet this demand? We’re already seeing OEMs starting to think about how to achieve these targets for recycled content. For many, it’s an important part of their wider ambitions to decarbonise the production of EVs. Altilium will be producing battery cells with UKBIC next year that will comply with the EU’s new regulations, so we’re going to play an important role in ensuring OEMS meet these targets. One of the challenges is you have to build the recycling capacity at the largest scale and the scrap isn’t ready yet. But that is going to change over time. By 2040, we see that maybe 50% of the lithium will come from recycling, there’ll be enough scrap in the system. |
➡️ The UK EV battery value chain is struggling to take off, and we’re yet to see a new gigafactory project materialise. What do you see as the major headwinds in the country? How can these be addressed? Actually, we’re pretty positive about the UK market. If we look at battery manufacturing, the commitments from ASEC and Tata will get us to over 75 gigawatt-hours (GWh) by 2030. That’s getting close to the 90 GWh of batteries that the APC says the UK will need to support production of nearly one million BEVs per year. If the West Midlands Gigafactory secures investment as well, then we could be looking at around 130 GWh by 2030. The question now is around the supply chain for the critical battery minerals needed for these gigafactories. To meet the APC’s forecast demand, the UK will need over 160,000 t/y of CAM. One of the challenges is that these minerals are geographically concentrated in certain countries and the refining of these minerals is controlled by China. So the UK needs to build a domestic supply chain and a circular economy for critical minerals. We need to build the hydrometallurgical refining capacity and keep the black mass in this country. We don’t just want to produce battery raw materials and send them somewhere else. We want to pass it back to a UK gigafactory and keep that circularity, so we have industrial resilience. |
➡️ There certainly is a business case for battery recycling and CAM manufacturing. What would you identify as major tailwinds? We have a number of regulatory tailwinds in this business. For example, we have the EU battery regulation, which includes collection targets for end-of-life batteries, minimum recycling efficiencies, and from 2031 new batteries will have to contain a minimum level of recycled nickel, lithium and cobalt. Essentially automotive companies are being regulated to close the loop on a battery supply chain. We see that the UK is very unique in terms of being an island. We don’t see a scenario where end-of-life EV batteries will be transported to refineries in Europe. This is a domestic industry that will be built in the UK. We have the second largest adoption of EVs in Europe and we have a gigafactory complex of battery manufacturing starting in the UK. Wherever there are high volumes of EV uptake and gigafactory production there needs to be battery recycling. |
➡️ Finally, if you could ask the new UK government anything, what would that be? The UK government has been transformational in supporting Altilium, to develop green processing technologies, to scale the technology. We hope that support continues when we’ve got to build physical infrastructure. The nature of this energy transition is that the capex is big. Building gigafactories, building at-scale battery recycling, the amount of money you need is kind of breathtaking. There needs to be public government money involved, we see that with the Inflation Reduction Act in the US. There needs to be a battery recycling system built in the UK and the first projects probably need some government money to support them, alongside other sources of funds. So we’re hoping to see the new government continue to support companies such as Altilium, to build the infrastructure which is critical to the UK’s energy transition. |
Truly global, user-friendly coverage of the steel and related markets and industry that delivers the essential information quickly while delivering on most occasions just the right amount of between-the-lines comment and interpretation for a near real time news service of this kind.
Anonymous
Very good overview of the weekly steel market.
Anonymous