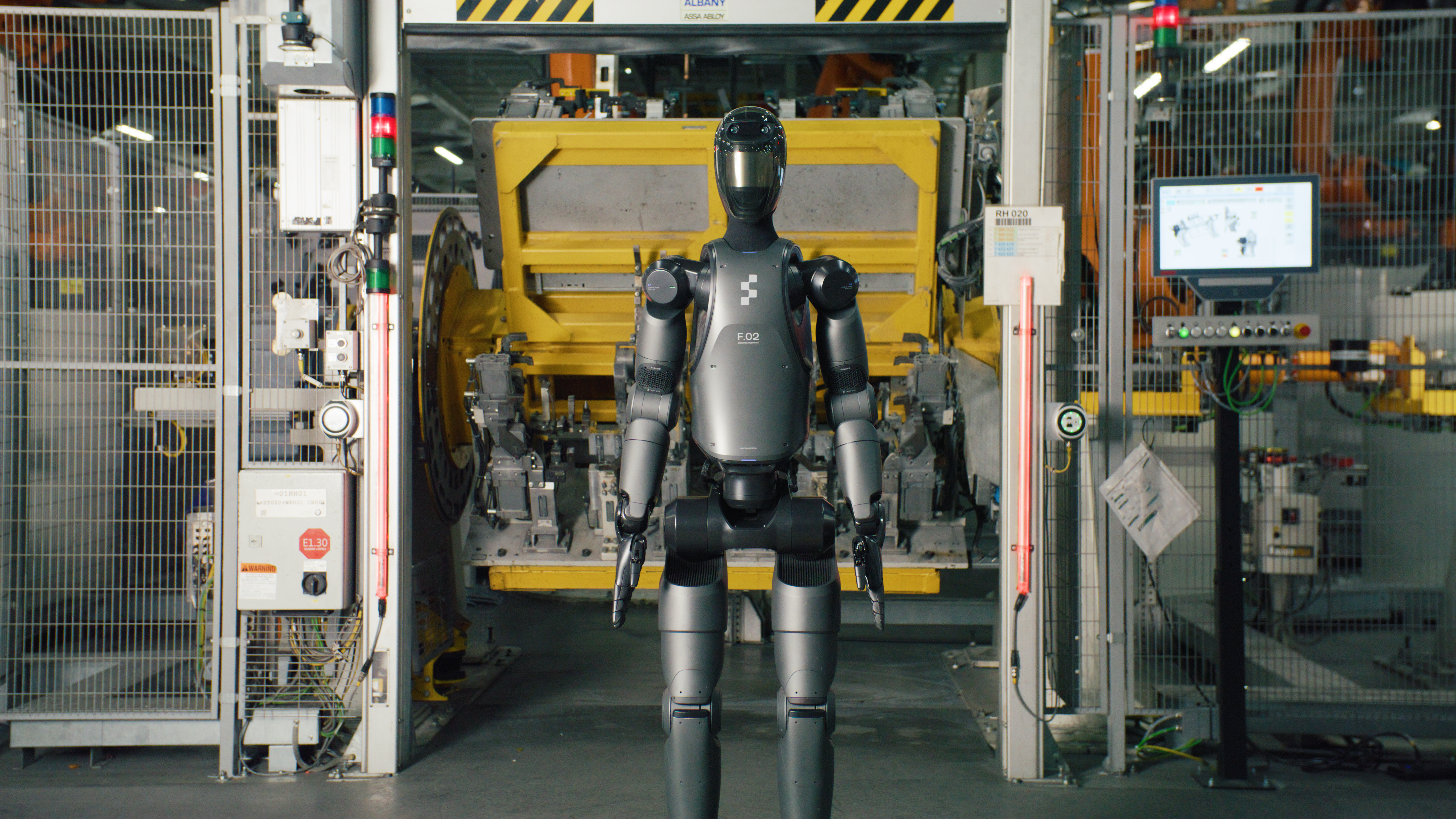
AI, humanoid robots set to transform automotive industry
Artificial intelligence (AI), 3D printing, robotics and electrification are transforming the global automotive industry in a move to increase efficiency in both automotive manufacturing and supply chain.
According to analytics company GlobalData, five key development areas in automotive manufacturing are driven by AI: supply chain management; vehicle testing; vehicle production & assembly; prototype development; and design & concept development.
“Manufacturers use AI-generated design algorithms to explore multiple design possibilities, optimising vehicle weight, strength, packaging, and performance. This leads to the creation of lighter, more efficient vehicles,” comments Vivek Kumar, automotive project manager at GlobalData.
Additionally, AI is also powering robotic machines, which can perform more complex tasks that are laborious for human workers. As a result, companies can achieve higher manufacturing quality, reduce wastage and increase output, Kumar says.
On Tuesday, BMW Group said it is exploring the use of humanoid robots in production for the first time. During a trial run at its Spartanburg plant in the US, the so-called Figure 02 humanoid robot inserted sheet metal parts into specific fixtures, which were then assembled as part of the chassis.
The robot, produced by California-based firm Figure, must be “particularly dexterous to complete this production step,” BMW says in a statement to Kallanish. The carmaker is currently evaluating how these robots can be used safely in automobile production.
“With the BMW iFACTORY, the vision of the production of the future, the BMW Group is always on the lookout for new technologies. Efficiency, digitalisation and sustainability are central to this vision to realisation,” the company adds.
The carmaker explains that during the trial run, which lasted a few weeks, it gained “valuable knowledge” of what requirements must be met to be able to integrate so-called multi-purpose robots in an existing production system. “This includes how humanoid robots communicate with the system under real conditions,” it notes.
As plants gradually convert to vehicle electrification, carmakers are also taking advantage of other technologies such as 3D printing. The process can accelerate the prototyping and production phases, reduce material waste, and lower overall production costs.
EVs require a smaller number of components than internal combustion engine (ICE) vehicles. This reduction in components will significantly impact the variety and quantity of parts produced by suppliers, according to GlobalData.
“These manufacturing trends are driving changes in every aspect of the automotive industry, fundamentally transforming its foundation,” says Kumar. “The future of the automotive industry lies in the seamless integration of advanced software solutions… Over the next five years, significant improvements in the automotive manufacturing and supply chain will be required to accommodate this development at the vehicular level.”
The Figure 02 robot is deemed to be the world’s most advanced humanoid robot currently available on the market. It’s ideally suited for use in areas with physically demanding, unsafe, or repetitive processes.
Following the trial run, no robots are in use at the Spartanburg plant. BMW Group notes there’s no definite timeline for bringing Figure robots back to the plant. It’s currently working with Figure to analyse data and train capabilities.
Truly global, user-friendly coverage of the steel and related markets and industry that delivers the essential information quickly while delivering on most occasions just the right amount of between-the-lines comment and interpretation for a near real time news service of this kind.
Anonymous
Very good overview of the weekly steel market.
Anonymous